The Ultimate Light Weight Aluminum Casting Guidebook: Step-by-Step Recommendations for Success
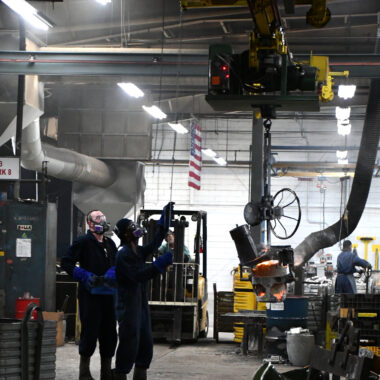
Security Safety Measures for Aluminum Spreading
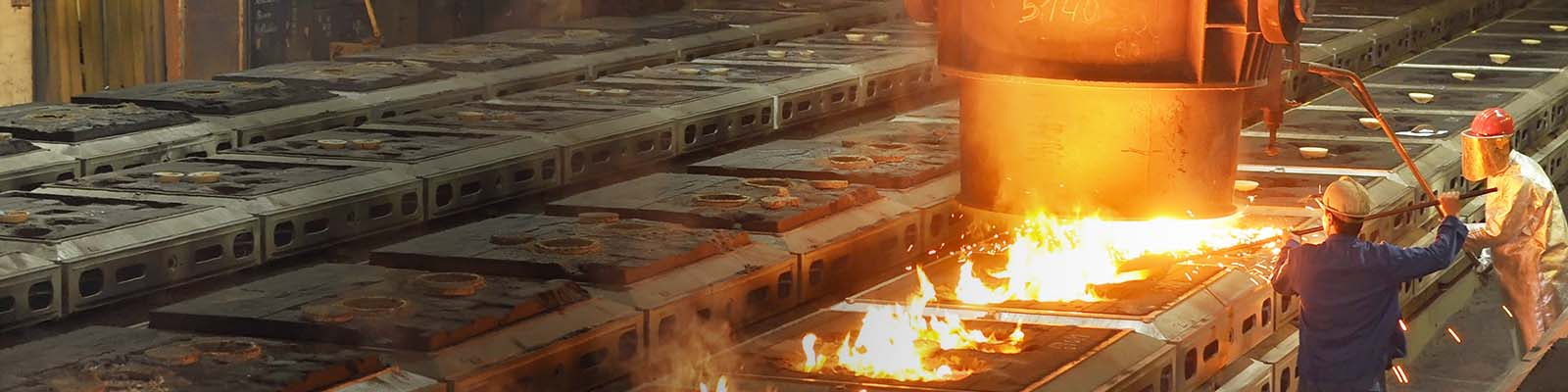
Additionally, maintaining a neat workspace devoid of clutter can protect against tripping hazards and assist in the movement of employees throughout casting procedures. aluminum casting illinois. Proper training in taking care of molten aluminum and operating casting devices is vital to minimize the threat of mishaps and injuries. Routine tools upkeep and inspection need to be performed to identify and fix any type of prospective safety hazards quickly
Setting Up Your Light Weight Aluminum Casting Work Area
Establishing a reliable and risk-free work space for light weight aluminum casting is vital for ensuring smooth operations and decreasing potential dangers. Prior to setting up your office, make sure that it is well-ventilated to avoid the buildup of damaging fumes created throughout the casting procedure. Organize your devices and devices in a logical way, maintaining them within simple reach yet likewise preserving clear pathways for activity around the workspace. It is important to have an assigned area for every phase of the spreading procedure, such as pattern making, mold preparation, and steel pouring, to simplify operations and stop cross-contamination. Furthermore, ensure that your workspace is furnished with fire extinguishers and emergency situation safety devices, and that all employees are educated in proper safety procedures. Use heat-resistant materials for work surface areas and floor covering to prevent damages and crashes as a result of heats. By thoroughly establishing and intending up your light weight aluminum casting workspace, you can produce a productive environment that focuses on safety and security and efficiency.
Selecting the Right Light Weight Aluminum Alloy
To guarantee optimal casting results in your safety-focused and efficient office, choosing the ideal aluminum alloy is paramount. Different light weight aluminum alloys use diverse features such as toughness, sturdiness, warm resistance, and my company machinability. The option of alloy relies on the particular requirements of your spreading job.
One typically used aluminum alloy for spreading is A356. This alloy displays excellent fluidness, making it optimal for complex castings with thin walls. A356 also has good corrosion resistance and mechanical buildings, making it appropriate for a wide variety of applications.
If greater stamina is needed, 7075 aluminum alloy is a prominent selection. Known for its high strength-to-weight proportion, 7075 is commonly used in applications where toughness is crucial, such as aerospace components.
For projects that involve high-temperature atmospheres, 319 aluminum alloy is a great option because of its exceptional thermal conductivity and resistance to thermal fracturing.

Step-by-Step Aluminum Spreading Process
Starting the aluminum spreading procedure involves careful preparation and adherence to an accurate series of steps to guarantee the production of top notch spreadings. The very first step is pattern creation, where a replica of the end product is made from plastic, steel, or timber. This pattern is then made use of to create the mold and mildew, which can be made from products like sand or plaster. When the mold and mildew is prepared, it is time to thaw the light weight aluminum in a heating system at temperatures surpassing 1200 ° F.
After getting to the preferred temperature, the molten aluminum is poured into the mold and mildew tooth cavity. This action calls for care and precision to stay clear of issues in the final casting.
Throughout the entire procedure, careful tracking and quality assurance measures must be implemented to guarantee the last light weight aluminum spreading satisfies the called for specifications and standards.
Tips for Refining Your Spreading Technique
In refining your aluminum spreading strategy, careful interest to information and adherence to specific actions are critical to ensuring the manufacturing of This Site high-quality spreadings. One essential idea for developing your casting strategy is to carefully prepare the mold and mildew and guarantee it is tidy and correctly coated with a launch agent to assist in the easy removal of the casting. Checking the spreading for any flaws and making essential adjustments to the process will assist you enhance and best your light weight aluminum casting technique over time.
Conclusion
To conclude, following appropriate security precautions, establishing an ideal office, picking the right aluminum alloy, and faithfully following the step-by-step spreading process are essential for successful aluminum spreading. By focusing on these crucial elements and incorporating tips to fine-tune your strategy, you can achieve exceptional outcomes in your light weight aluminum casting jobs.
From security preventative measures to refining casting strategies, this guidebook serves as a sign of expertise for those venturing into the world of aluminum spreading.
Starting the aluminum casting process involves meticulous prep work and adherence to an exact series of actions to guarantee the manufacturing of high-quality castings.In refining your aluminum casting method, thorough attention to information and adherence to exact steps are vital to making certain the production of high-quality castings. One critical suggestion for refining your spreading technique is to very carefully prepare the mold and guarantee it have a peek at this website is clean and correctly coated with a launch representative to help in the simple removal of the spreading. Inspecting the casting for any blemishes and making necessary modifications to the procedure will certainly assist you boost and excellent your light weight aluminum spreading method over time.